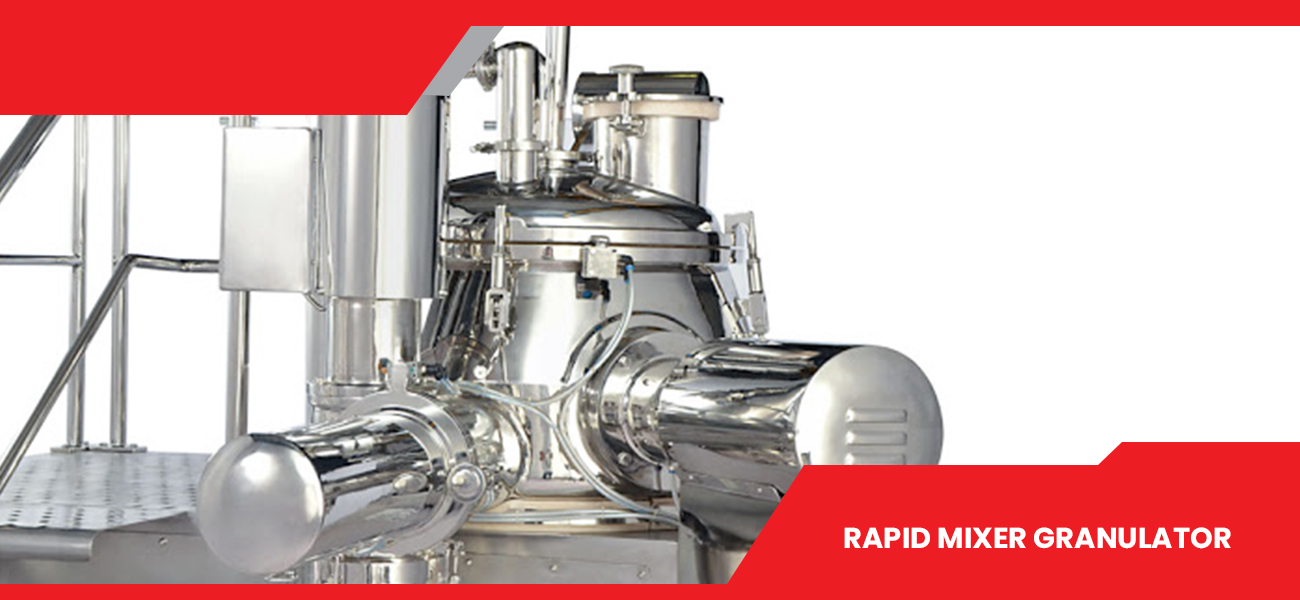
- Home
- Rapid Mixer Granulator
Rapid Mixer Granulator
Application :
“ PHARMA FAB INDUSTRIES “ Rapid Mixture Granulator (RMG) or also known as The High Shear Mixer Granulator used for process of fast dry & wet mixing, homogenizing, humidifying and granulating of the powder in Pharmaceutical, Chemical, Cosmetic, Food, Plastic, General Mixing Industries.
Process :
High Shear Mixer Granulator is characterized by the Compact construction, Modern design and all the user and maintenance friendly attributes which form the Ergonomically design aspects are essential for a wide range of application.
The High Shear Mixer Granulator performs Dry mixing & Wet granulation by basic design of the special four arm of the mixing impeller and sequences of the mixing process in the cylindrical mixing drum with rounded connection to the base plate, achieve another special effect. The mixing process runs without varying pressure zone in the volume of mixing product. Separately driven multiple choppers can effectively intensify the mixing result in particular when liquid or paste components are added. During humidifying and granulating process of the products the chopper controls and regulates the granular spectrum and structure of the granules according to the product, chopper shape and time. The HSMG system requires only small quantities of granulating liquid or pastes to obtain the required granulate structure. This reduces the amount of drying energy required.
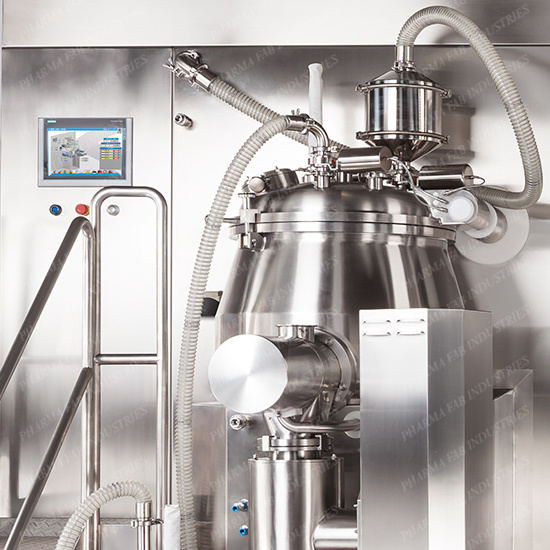
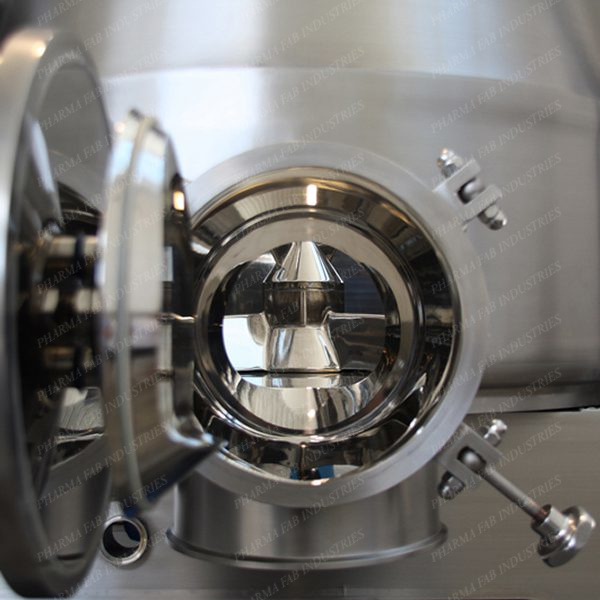
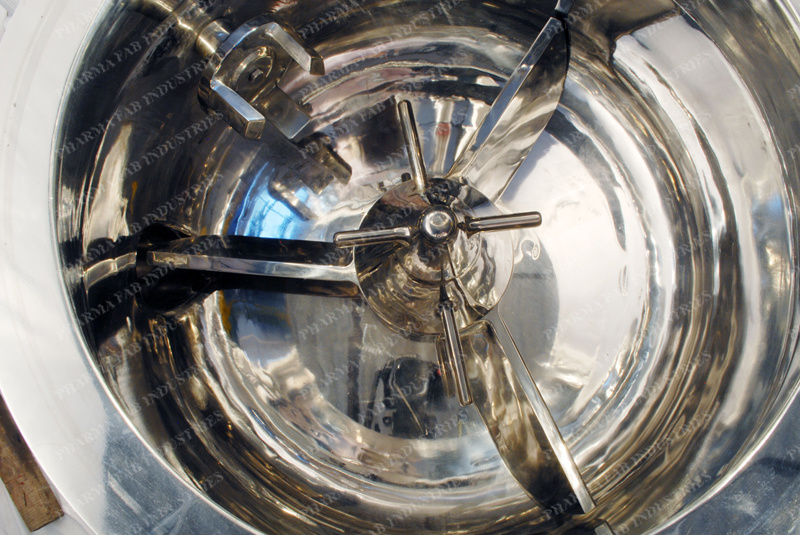
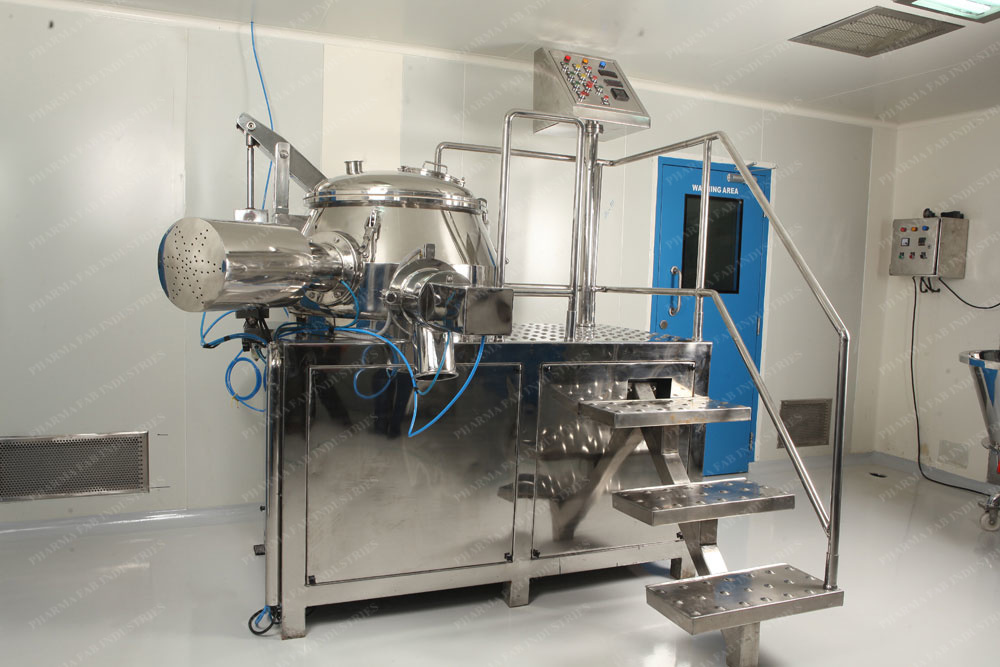
Salient Features of Rapid Mixture Granulator:
- It is available from 50 Litres capacity to 600 Litres capacity . Available from Lab Model to Production level model
- Design as per GMP and cGMP model
- MOC : SS 304 , SS 316 , SS 316 L Quality
- It is used for High speed Mixing & Granulating
- All Product Contact parts SS 316 / 316L & Non Contact parts SS 304.
- Automated mixing and granulating process in single bowl.
- High Precision mixing and granulation with Short Batch Time, Problem free Cleaning and Residue Free of Discharge.
- Unique design with four arm mixing impeller with blade angle to pushing product radically outward.
- Chopper blade designed to cuts lumps and make uniform granules.
- Dual speed mixing impeller for mixing and intensify the chopper for granulating.
- Flush fitting discharge plug is electro pneumatically operated.
- Air pursing for seal for both shafts.
- All internal & external surfaces will be polished for smooth and ease in cleaning.
- All fabrication will be as per relevant standards and will adopt good engineering practices.
- All welded joints will be neatly ground to give a smooth finish.
- Easy and Safety in operation.
OPERATION
- Dry powders are first loaded into the RMG by vacuum or gravity (total containment).
- RMG’s are extremely quick and efficient mixers of dry powders. Dry mixing is the first step of the process.
- After the products are mixed by means of the bottom drive rotating impeller, a binder is introduced into the product.
- The binder can be added in dry form or sprayed in as part of a binding solution.
- Spraying occurs though one or more spray nozzles and is quickly dispersed into the product by the mixing action of the main mixing tool (impeller) and the chopper blade.
- The chopper blade, which is positioned in the highest circumferential area of the product aids in de-lumping.
- The end point of the granulation is detected by ammeter. Granules are then easily and automatically discharged from a port in the bowl’s side. The wet granules are generally milled as they come out of the granulator.
SPECIFICATIONS
The rapid mixer granulator consists of following main components:Mixing Bowl:
The mixing bowl is circular in shape with flat base and top portion conical in shape which is made out of SS316 with highly polished internal and external surfaces. It consists of following parts:- Main agitator
- Chopper
- Discharge
Lid :
Lid is made out of SS316 with non contact parts in SS304, matching the bowl flange with hermetically sealing gasket provided with safety interlock. Lid can be opened by Counter-weight arrangement or with the help of pneumatic lifter(optional). Lid is provided with view port. It has small diameter port for:- Addition inlet by gravity and
- Attachment of spray nozzle
- Air vent with filter is provided.
Control panel
Control panel consists of:- HMI
- Main Switch
- Rotary switch
- Emergency push button
- Hooter with flash
- Pressure gauge
- Tower lamp
- NO/NC contactors
Power panel
Power panel consists of:- MCB
- PLC
- RYB Indicators
- Ammeter
- Emergency stop switch
Pneumatic Panel:
- Pressure switches
- Pressure gauges
- Solenoid valve and solenoid coil
- Lubroset with oiler
- Air filter unit
- Fine filter comb.
- Connector
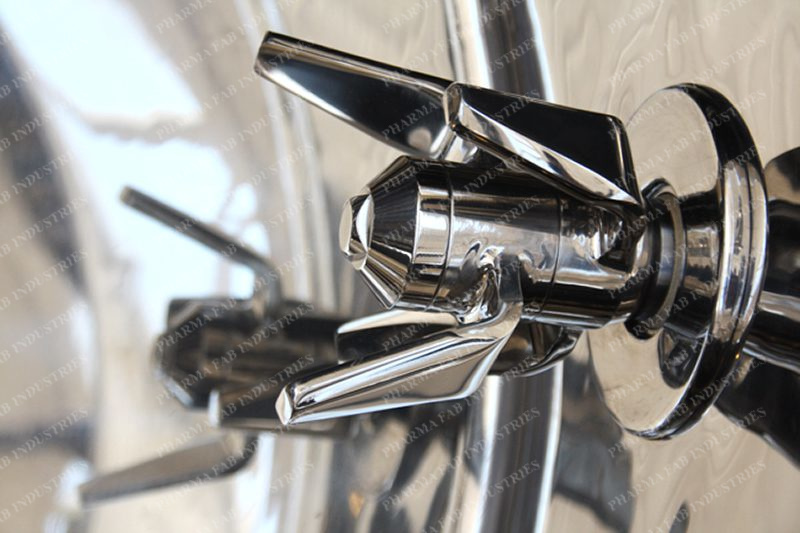
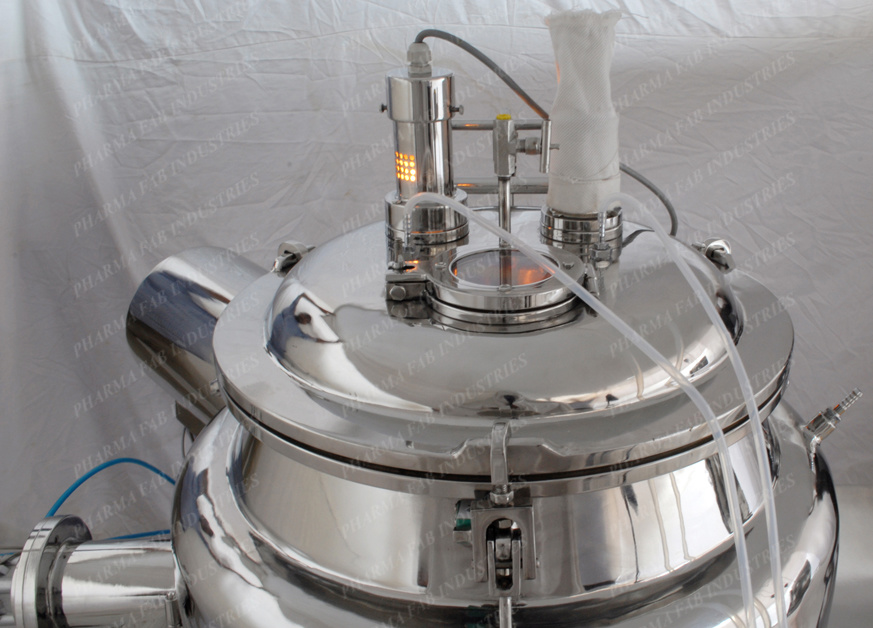
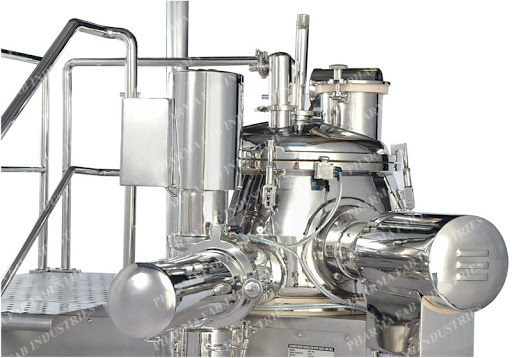
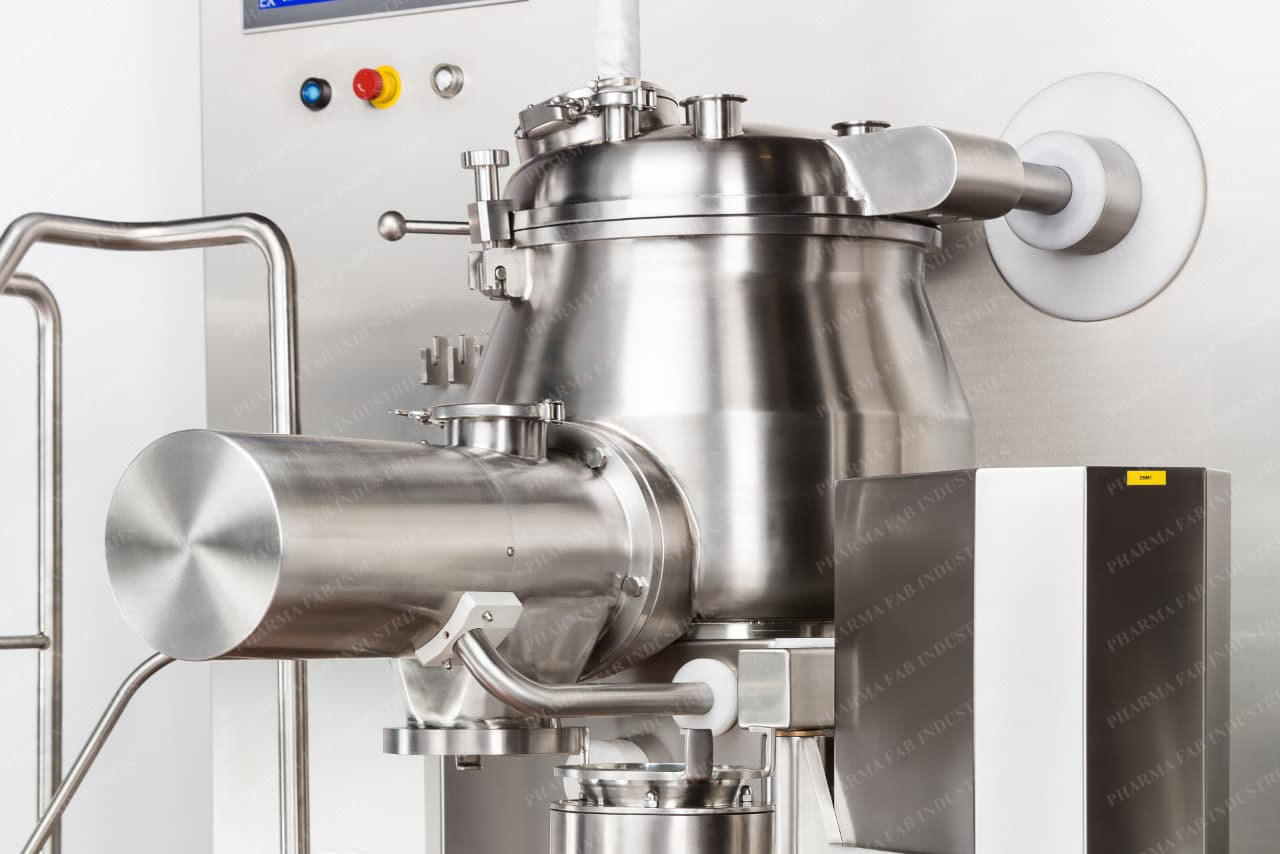
Optional Features :
- PLC Controls with HMI touch screen,
- Co- Mill arrangement can be provided.
- Inline Milling at discharge,
- Variable speed drive for main impeller and chopper.
- Product bowl Jacketing for heating/ cooling and vacuumized mixing process.
- Binder adding by spraying system with peristaltic pump.
- Material charging by bin loader with IBC.
- Flame proof motor and electrical.
Safety Features :
- Total drive transmission system enclosed
- Limit switch installed in the top lid ensure lid is closed
- Air pressure switch installed to ensure pressure is in limit.
- Limit switch installed at discharge to ensure product container underneath of discharge.
- Overload relay Protection and Emergency stop button