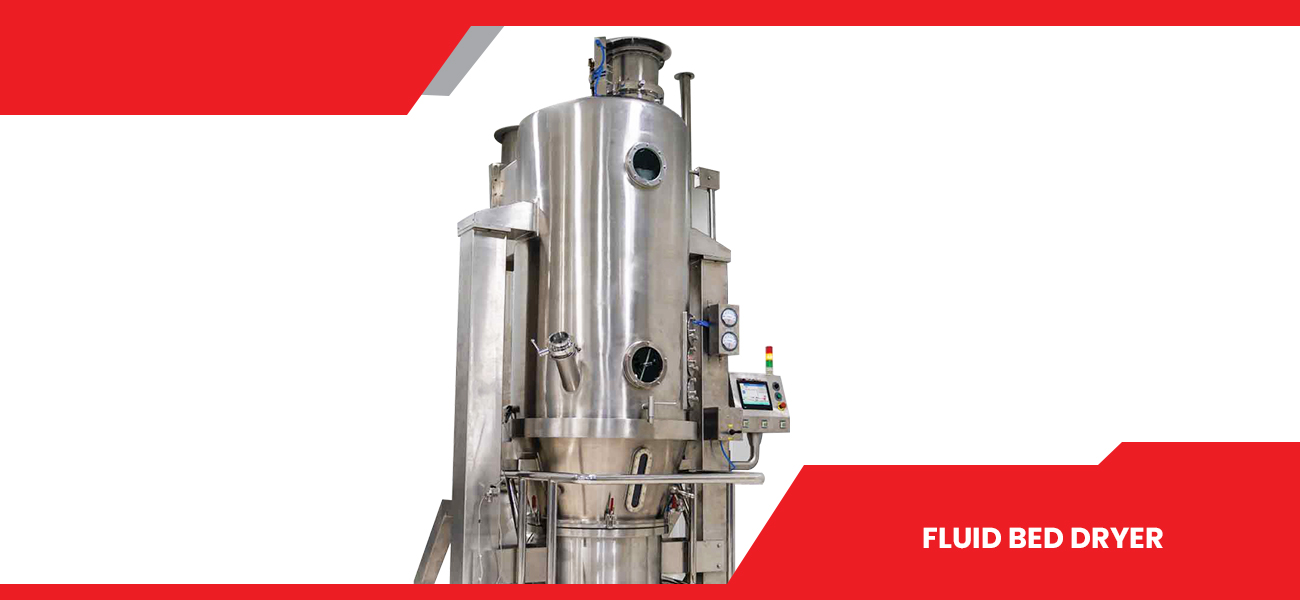
- Home
- Fluid bed Dryer
Fluid bed Dryer
CAPACITY
- Fluid bed dryer comes with range of capacities as per our customer’s requirement.
- Capacity range: – 5 Kg to 500 Kgs
Process
” PHARMA FAB INDUSTRIES “ Fluid Bed Dryer involves fast drying, cooling and agglomeration of particulate materials. It is ideal for heat sensitive and non heat sensitive products in Pharmaceuticals, Chemicals and Biochemical, Food and Dairy Industries.
The Fluid Bed Dryer have a bed of solid particles which are fluidized by passing a stream of air upward through a specially designed perforated sheet. The upward velocity of air is so maintained so as to slightly lift the solid particles and set them in motion. This motion can be utilized to bring about mixing as well as forward movement of the solids particles. The air is heated and the process hot air evaporates the fluid and dries the solids. Fines get agglomerated to larger granules particles thus providing large size.
The wet material is loaded into the product container which is provided with air distributor plate and Dutch weave mesh. Fresh air-to-product-contact is filtered by means of 3-Way filtration process i.e. through coarse filter , 5 micron filters and the HEPA Filter is heated by means of heater (steam or electrical). This hot air then passes through the product container, creating turbulence in the product and hence product moves up and down in the product container. Due to this the heat transfer is quick and the product is dried fast without appreciable heat loss. Filter bag prevents particle escaping from the dryer.
The machine is designed with correct volume of bowl, air velocity, direction and the temperature of the clean inlet air is maintained throughout the fluidization, retarding, and expansion chambers, filtration area, pitch of the perforations of the plate at the bottom of product container, the leak-proof fluidization space by proper sealing, material of the filters and process controls with electrical & pneumatically.
The uniform drying is achieved by exposing the full surface of every particles of the solid mass to the incoming high velocity hot air.
Option for the process parameters are controlled by using latest PLC controls with HMI touch screen thus making equipment operationally safe and eliminating the possibility of human error. The process consistency with batch records is maintained for every batch every time.
The equipment can be inbuilt CIP system gives a thoroughly cleaned equipment for every batch eliminating contamination of subsequent batches.
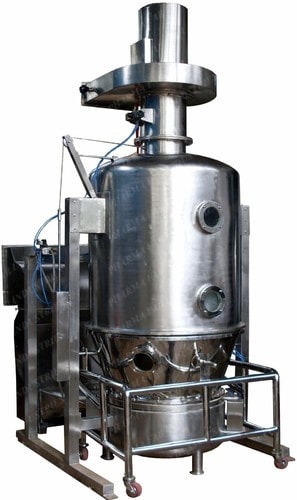
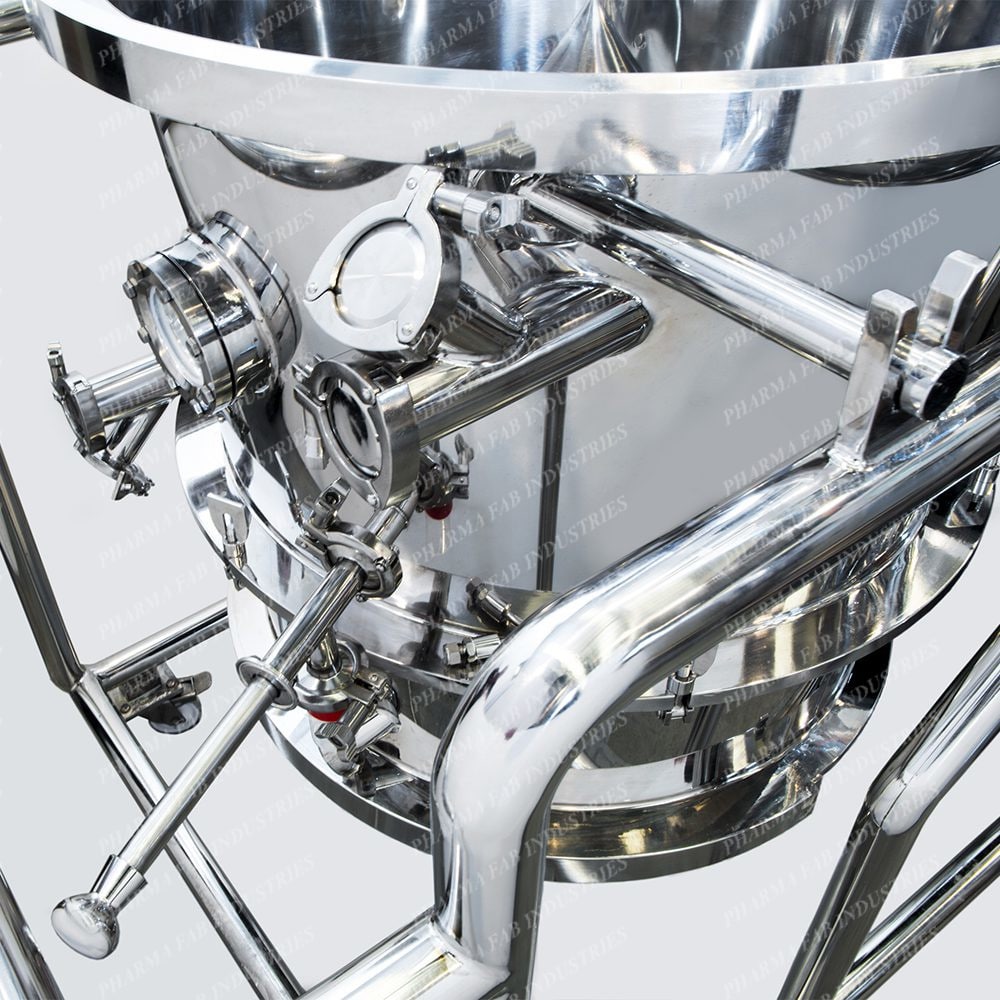
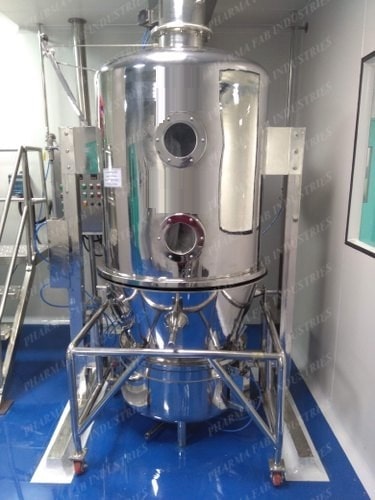
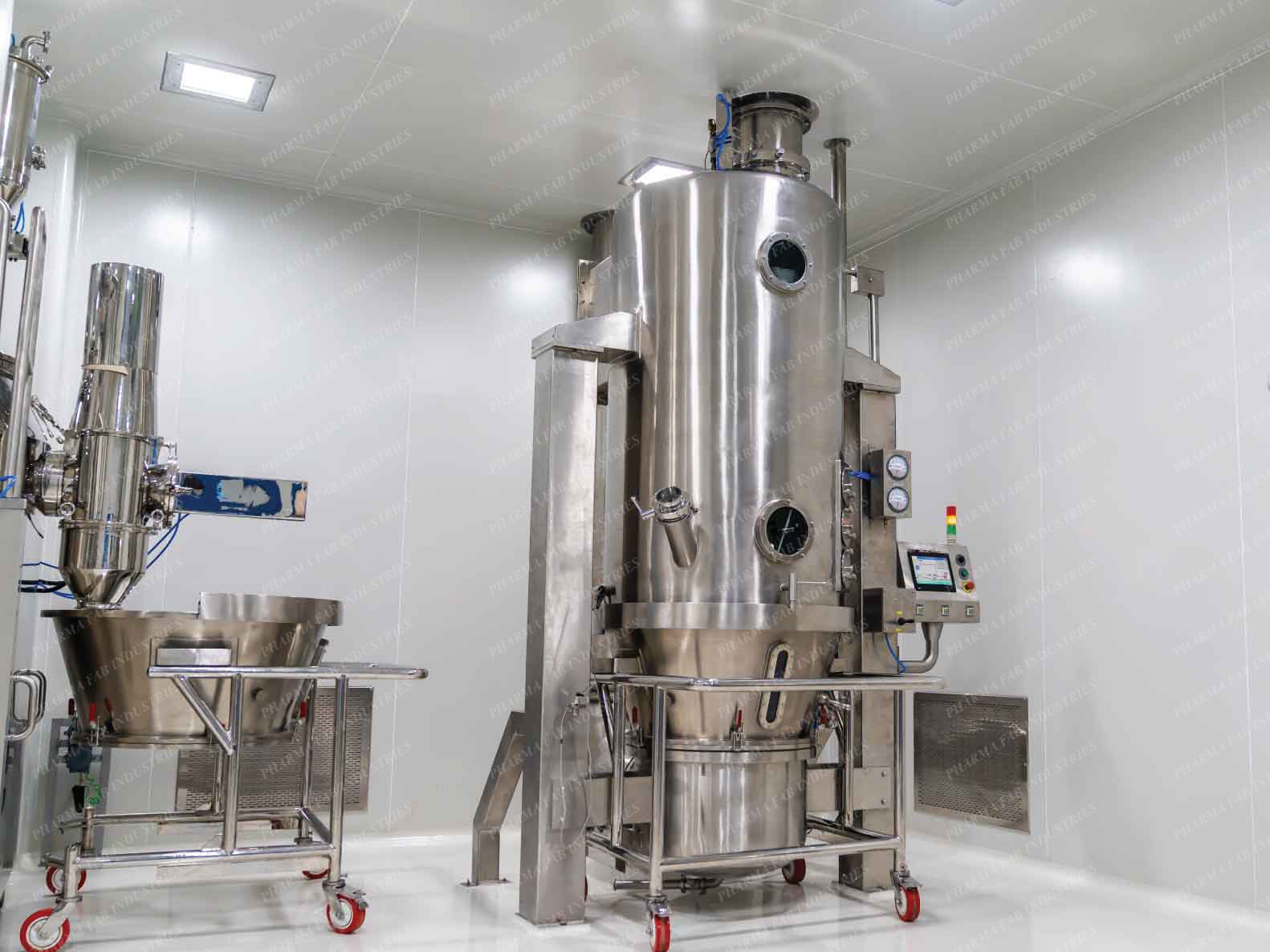
APPLICATION
- Suitable for drying humidity from powder raw material in Pharmaceutical, foodstuff, feed, chemical industries, etc
- Semi-liquid materials, large granules, small blocks and adhesive material.
- The materials that volumes vary during drying process.
- Fluid bed Dryer can be supplied with Upgradation to be used as processor(Vertical Spray / Bottom Spray Granulation)
- Pharmaceuticals granules or crystals containing free moisture can be easily dried as per customer’s requirement.
SALIENT FEATURES
- Design is cGMP – Current Good Manufacturing Practices compliance.
- All contact parts AISI 316 & non contact parts AISI 304.
- Monoblock Construction: Retarding chamber and expansion chamber are made in single piece construction to enhance cGMP and facilitate hygienic cleaning.
- Single piece construction with Integrated retarding expansion chamber cum filter bag housing
- Batch type dryer with available capacity 30 kg to 500 kg. Batch size
- Pneumatic Sealing of Filter Bag and Product container by inflatable silicon rubber tube.
- Pre air filtration by 20 micron filters and secondary by 5 micron.Final air filtration through HEPA (0.3 micron) filters as an optional features.
- Inlet Air handler with Air Filter- Micro, HEPA and Heat Exchanger Steam or Electric.
- Exhaust air blower with dynamic balance fan.
- High pressure backward curve blower.
- Built in Explosion vents and isolation valve protect equipment.
- Automatic Temperature controls for Inlet Air and Process cycle time controls.
- Washable filter media.
- Auto pneumatic filter bag shacking system.
- Electric and Pneumatic controls panel.
BOWL / PRO DUCT CONTAINER
Product bowl is a conical shaped manufactured form SS-304 grade stainless steel having stainless steel mesh support along with fine finish air mesh.
The product container Trolley is of Tubular construction made form SS-304 pipe mounted on polypropylene castor wheel (2nos fixed & 2nos. Swivel for maneuverability ) which imparts rigidity to carry the product container with the charged load.
The batch loading capacity is always higher in case of “Shree Bhagwati Pharma Machinery” Fluid Bed dryer, because of better fluidisation by varying the frequent shaking of the finger bags. Shaking period vary depending on the nature of products.
RUBBER GASKET
A solid ‘D’ shaped food type silicon rubber gasket is provided in the groove of the flanged joint (between the product container and the retarding chamber) to prevent any leakage of air with fines during operation.
Uniform Lifting Of Container
Product container is lifted by specially designed arrangement with the help of one centrically fitted pneumatic cylinder which ensures uniform lifting throughout the periphery of the container which ultimately gives uniform upward pressure to the solid ‘D’ shaped Rubber Gasket, thereby preventing any leakage during operation.
Auto Shaking Device
Pneumatic cylinder is used for auto shaking device of the finger bags is mounted on the body and is fitted with a wire rope made out of S.S. 304 guided by pulleys thus rendering the shaking extermely efficient. It also brings down the finger bags to such a level that these can be inspected very easily form the bottom of the retarding chamber. If the shaking is not efficent , the particles will be retained in the finger bags and there will be no proper fluidisation resulting in formation of lumps in the products container.
Top
Air Handling Unit
Blower and filter with heating arrangement are housed in the rear chamber . They can also be housed the services zone to avoid sound pollution as well as to avoid interference of the maintenance people in the production zone.
Air filter
Free standing unit constructed from aluminium anodisedl frame work (SS-304) with doubled skinned panels. All wallpanels are cross based for added strength . Quick release panels provided for inspection and maintenance access.
The air intake section has a full face external flange for attachment of angle intact, or and extended inletair duct.
Inlet system comprssiong of 20Micron washable filter. followed by 5 micron prefilter, then pass through , heating coil section containing a full air duct steam operated heater battery, constructed with stainless steel tubes and headers and a steel casing (SS-304). The moving process air passes through the steam heater to achieve the desired temperature. to match the inlet to the processing unit.
PT 100 temperature sensing probe will be fitted into the air Transtion duct and will be connected upto the control panel.
Blower
- Centrifugal type blower fan with dynamically balanced impeller and backward curved blades.
- All Stainless steel construction.
- Direct coupled non—flameproof electric drive. Anti – vibration mounting and independent sub-supportframe.
Explosion Vent
As per international practices the equipment is provided with a rapture disc as measures of explosion Vent, Tested at 2 Bar pressure, mounted on the side of the dryer.
Earthing Device
A std designed earthing device spring type is provided with the dryer however intrincically safe earthing device with low voltage relay is also available.
Electro Pneumatic Control Panel
- A free stading steel control panel having the following controls.
- Inlet air temperature controller.
- Exhaust air temperature indicator
- Product bowl lifting & lowering valve.
- Process air Damper regulation
- Blower motor, start & stop.
- Compressed air pressure quages.
- Filter bag shaking timer
- Solenoid valves etc.
Programme Logic Control System
Semi-automated and fully automated PLC and PLC / PC control system are available for selection at an appropiate level of additonal cost. (OPTION)
Optional Features :
- Additional Product container.
- Controlled by Advance PLC controls with touch screen or with printer
- Double scan Air Heating Unit with Dehumidifier.
- Steam or Electric Heater
- Pneumatic bag shaking arrangement
- Exhaust AHU with Filter
- Online sampling port .
- Silencer at exhaust blower.
- CIP – WIP system.
- Explosion proof motor and push button.
- Solid Flow Sensor : To detect leak on filter bags to avoid material loss and air pollution.Differential Pressure gauge for filter.
- Standard model machine with contact parts in S.304 & Non contact parts epoxy painted.
Safety Features :
- Product Bowl interlocking mechanism.Automatic Temperature & controls, Process cycle controls.
- Solid Flow Control system
- Explosion flap ensure at retarding chamber.
- Safe earthling system for static current.
- Air pressure switch installed to ensure pressure is in limit.
- Overload relay Protection and Emergency stop button.
NOTE: For inflammable products, steam heating and flame proof motor essential.
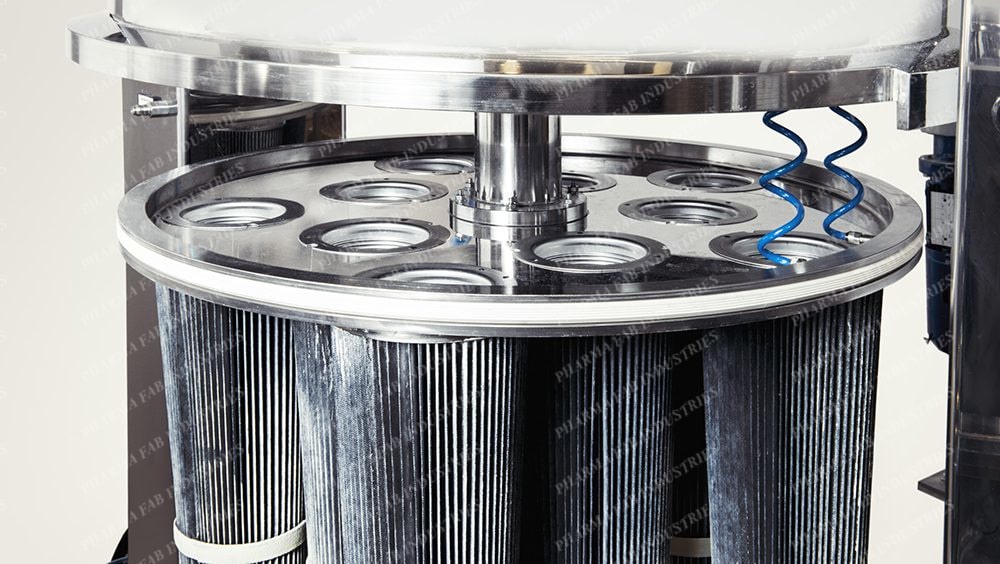
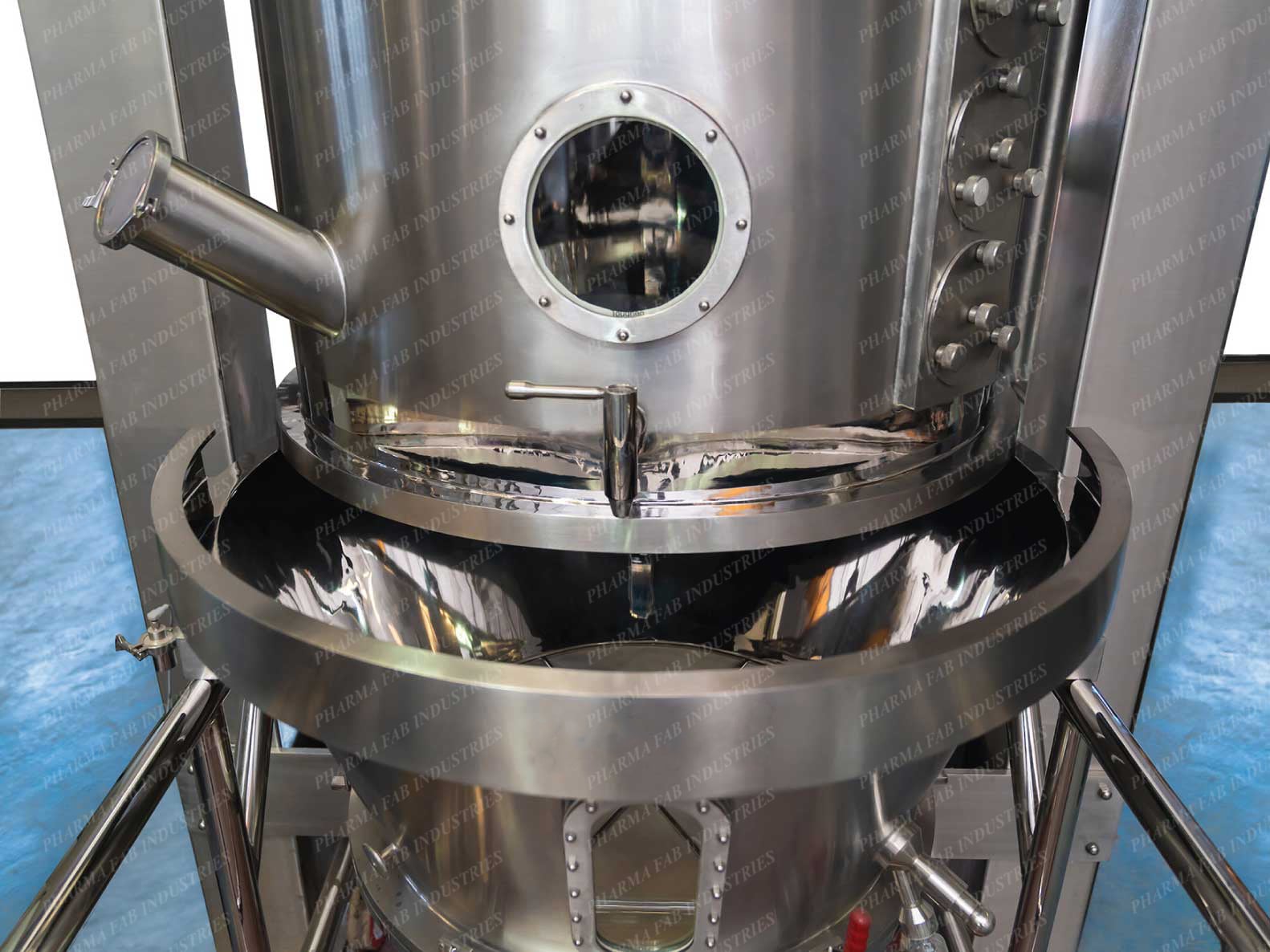